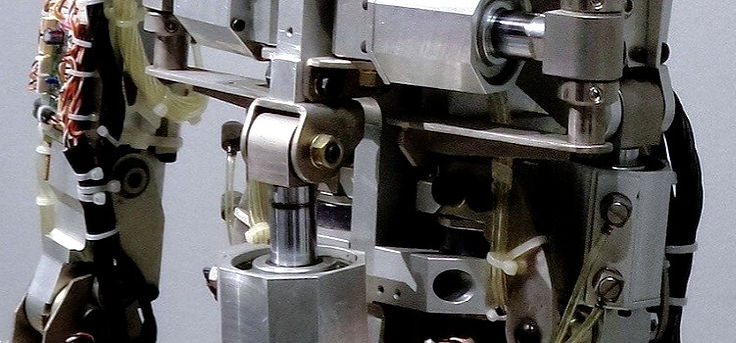
HELLO, I'M
Thomas Kuan.
Master Student at Stanford University
Mechanical Engineering.
About
MY BACKGROUND
With a passion for Mechanical Design, Robotics, Automotive Engineering, and all things that can make the world more convenient, I have both the skill set and professional background necessary to dive deep into the technology world. As an upbeat, self-motivated engineer with excellent design skills, I envision an exciting future in the industry.
Browse my site to see all that I have to offer.
Education Background
2019–2021
Stanford University
Master of Science; Mechanical Engineering
Areas: Mechanical Design, Robotics, Manufacturing and Product Realization
2014–2018
National Tsing Hua University
Bachelor of Science; Power Mechanical Engineering
GPA: 4.07/4.3 (3.92/4.0)
Ranking: 3/97
Honors and Awards
Academic Achievement Awards of National Tsing Hua University
2014--2018
-
Received Academic Achievement Awards 4 times.
Senior Capstone Projects Competition
Dec. 2017
-
Project: Power Exoskeleton for Motion Recording and Reproducing.
-
Received Second Prize and “The Most Popular” award out of 40 teams.
ARM Design Contest 2017 Taiwan District
Nov. 2017
-
Received Honorable Mention Award out of 200 teams in annual ARM Design Contest.
EUROBOT 2018 WORLD CUP
May. 2018
-
Leader of the Mechanical Design Group.
-
Final World Rank: 24th (Team DIT Robotics).
Opto-Mechatronic Systems Design Contest
Jun. 2017
-
Project: T-MOUSE.
-
Received First Prize out of 12 teams.
Projects
Power Exoskeleton for Motion Recording and Reproducing
-
Designed a power suit that records angular configurations of the shoulder joint when a person demonstrates motions, then users can wear it to reproduce the recorded motions. Its main purpose is to increase the accuracy and efficiency of shoulder rehabilitation.
-
Designed it with 3 revolute joints to synthesize 3-DOF rotational motions of the spherical joint (shoulder joint) with Euler-angles convention, and equipped each axis with a rotary encoder for recording data, drivetrain mechanisms for actuating, and safety clutch mechanisms for disengagement.
-
Designed kinematic mechanisms, mechanical components, and transmission drives.
EUROBOT World Cup
-
Designed and built two autonomous robots to complete several specific tasks.
-
Designed the chassis powertrain and task mechanisms of the robots.
-
Derived kinematic and dynamic equations of the powertrain to evaluate how to optimize the integration of our mobile robots.
-
Leader of Mechanical Design Group.
T-MOUSE
-
A convenient and contractible Mouse that can reduce 57% thickness after contracting.
-
Designed the detailed mechanisms and manufactured the prototype.
Parallelogram Robotic Arm Project
-
Designed a 3- degree of freedom Robotic Arm that can grip objects weighing 1.8 kg.
-
The design features with parallelogram linkages that can reduce the moment of inertia and lower the center of mass.
-
Higher structural stiffness, larger workspace, and higher payload ability compare to regular serial robotic arms.
Modular Vehicle Powertrain and Chassis Design
-
Designed a small automobile chassis and transmission systems with CAD software.
-
The driveline and differential systems are designed in a way that makers can easily prototype with 3D-printing and machining.
-
Robotic arms, cameras, and other equipment can be integrated with this chassis and powertrain module design.
Hub Motor Module Mechanical Design
-
Designed a hub motor module consists of compact planetary gear sets to magnified the output torque.
-
This hub motor module concept can be used for wheel-hub motors in electric vehicles or joint actuators in robotic arms.
-
Designed the output flange with convenient studs and threaded holes for wheel mounting or serial robotic arm assembly.
Mobile Soccer Robot
-
Designed a mobile robot that can play robot soccer games.
-
Designed the gripper mechanism which features a much larger workspace by synthesizing the optimal coupler curve.
Cam Mechanisms Profile Generator
-
Programmed a set of MATLAB codes that can generate profiles and curves (including position, velocity, and acceleration characteristics) of cam mechanisms.
-
This generator can automatically fit the desired displacement points and the corresponding rotation angles specified by user inputs.
-
Engineers can utilize this cam profile generator to design pick & place motion of automation systems, gaits of walking quadruped robots, or other related applications.
Leg Mechanisms Design using Function Generator Synthesis Method
-
Developed a geometry generator that can help designers to create linkage mechanisms in GeoGebra.
-
This geometry generator can synthesize linkage mechanisms that pass through three arbitrary points specified by the users.
-
The generated mechanisms are mainly used for robot leg mechanisms or automation systems that follow specific paths.
Project Gallery
Skills and Knowledge
-
SolidWorks
-
AutoCAD
-
Autodesk Inventor
-
MATLAB
-
ANSYS
-
CATIA V5
-
Arduino
-
GeoGebra
-
Simulink
-
CAD/CAM
-
Robotics
-
Mechanisms Design
-
Mechatronics
-
Automotive Engineering
-
GD&T
-
Finite Element Analysis
-
Rapid Prototyping
-
Kinematic Synthesis
Other Experiences
ASME SPDC 2017 Contest in Taiwan District
Mar. 2017
-
Referee and Director of Planning
-
Evaluated the robots of each team and determined the points they got.
DIT Robotics
2014-2018
-
Leader of Mechanical Design Group
Research Experience at UC Berkeley
Jun-Aug. 2017
-
Assisted a super-capacitor project
-
Designed and built a car model that is driven by the super capacitor.
Student Association of Department at NTHU Power Mechanical Engineering
2015-2017
-
Officer of Event Planning
ZU Education Hsinchu
Jan-May.2016
-
Designed lab instruments and science teaching aids.